振れという単語は,フライスカッタにおいて,複数備える刃先間の刃先位置の変動を示します.
また,振れには静的な振れと動的な振れが含まれており,その分類と原因には以下のようなものがあります.
・静的な振れ:工具回転がなくても存在が確認できる振れ
カッタボディやチップの形状精度
主軸の回転軸と工具中心軸の同軸度のずれ
主軸の姿勢誤差
・動的な振れ:工具回転があって初めて存在が確認できる振れ
主軸の回転中心と,回転系の重心位置のずれによる遠心力で生じる変形
要するに,ダイヤルゲージを刃先にあてて,工具を手で回したときに測定できるのが静的な振れで,測定できないのが動的な振れです.
上記した以外にも要因は様々あると思いますが,本項の目的とは異なるので詳細は省きます.
静的,動的どちらでも刃先位置の変動という点では同じなので,以下の文章では両者を含んだ意味で「振れ」という単語を使用します.
また,振れには,軸方向と半径方向の振れがあります.
この2つの区別は重要なので,振れは軸方向と半径方向の2つの成分で構成されるものとして考えます.
ここで,振れの一般的な評価方法について述べます.
刃先位置の変動は,ダイヤルゲージやツールプリセッタで測定することが可能です.
刃数の分だけ測定した結果から,半径方向と軸方向の最大値と最小値の差を計算して,その値を振れとしています.
\( \Delta R_{conv} = max(R_{1}, R_{2},...,R_{n}) - min(R_{1}, R_{2},...,R_{n}) \)
\( \Delta H_{conv} = max(H_{1}, H_{2},...,H_{n}) - min(H_{1}, H_{2},...,H_{n}) \)
\( R_{n} \):N番目の刃先の半径方向位置
\( H_{n} \):N番目の刃先の軸方向位置
しかしながら,この方法で計算した振れの値では,情報の本質的な部分が失われており,その大小で切削抵抗のばらつきや面粗さへの影響を論ずるのはほとんど意味がありません.
確かに振れが0umと30umでは全く違うのですが,振れが10umと同じであっても,各刃ごとの刃先位置変動の仕方によって,切削抵抗のばらつきや面粗さへの影響が全く違うからです.
その理由について説明するために,この軸方向と半径方向の振れが,切削抵抗と面粗さに影響する仕組みについて考えます.
まず,切削抵抗への影響について考えます.
考察を簡単化するために,一刃かつセンターカットで切削しているときの切削抵抗を仮定すると,次式で計算されます.
\( F_{c} = K_{c} a_{p} f_{z} \)
\( F_{c} \):切削抵抗
\( a_{p} \):軸方向切込み量
\( f_{z} \):一刃あたり送り量
\( K_{c} \):比切削抵抗
上式は振れが一切ない場合を仮定しているので,ここに振れの要素を追加します.
フライス加工において,任意の切れ刃に注目したとき,その切れ刃は,一つ前の刃が加工した面を加工します.
つまり,現在加工している刃と,一つ前の刃の,切れ刃位置変動の相対位置が切削面積を考えるうえで重要になることがわかります.
ここで,N番目の刃とN-1番目の刃の刃先位置の相対位置を次式で計算します.
\( \Delta R_{relative,n} = R_{n} - R_{n-1} \)
\( \Delta H_{relative,n} = H_{n} - H_{n-1} \)
\( \Delta R_{relative,n} \):隣接半径方向刃振れ
\( \Delta H_{relative,n} \):隣接軸方向刃振れ
\( R_{n} \):N番目の刃先の半径方向位置
\( R_{n-1} \):N-1番目の刃先の半径方向位置
\( H_{n} \):N番目の刃先の軸方向位置
\( H_{n-1} \):N-1番目の刃先の軸方向位置
暫定的に,隣接刃振れと呼ぶことにします.
上式を使って,切削抵抗の計算式を補正すると,次式が得られます.
\( F_{c,n} = K_{c} (a_{p} + \Delta H_{relative,n}) (f_{z} + \Delta R_{relative,n}) \)
上式を用いて,切削抵抗に対する振れの影響を考察します.
振れというのは一般的な刃先交換式フライスカッタでは,そもそも0umから40um程度の範囲程度の大きさを持ちます.
これに対して,一般的な加工条件範囲では,軸方向切込み量は1mmから10mm程度,一刃あたり送り量は0.1mm/tから0.3mm/t程度になります.
よって,軸方向切込み量に比べて,一刃あたり送り量のオーダのほうが1桁小さいことになります.
ここで,軸方向切込み量:5mm,一刃当たり送り量:0.2mm/t,\( \Delta R_{relative,n} \):20um,\( \Delta H_{relative,n} \):20umを仮定して,その影響の差を試算します.
軸方向切込み量における,\( \Delta H_{relative,n} \)による変動割合は,0.4%です.
これに対して,一刃あたり送り量における,\( \Delta R_{relative,n} \)による変動割合は,10%です.
振れ自体の大きさは同じですが,切削抵抗変動への影響は25倍異なることがわかります.
そのため,振れによる切削抵抗変動への影響を抑え込むには,隣接半径方向刃振れを小さくすることが重要です.
よって,振れによる切削抵抗変動の大きさを調べたいのであれば,刃先位置の測定結果から,隣接半径方向刃振れを各刃において計算し,それらの最大値と最小値で評価すべきだと考えます.
次に,面粗さへの影響を考えます.
まず,フライス加工において,面粗さに影響する要因は,振れ,フェイスアングル,さらい刃長さ,さらい刃形状,一刃あたり送り量,刃数が挙げられます.
これらの因子が影響するために,転削加工においては,旋削加工のような面粗さの理論式を作ることができません.
特に,フェイスアングルや振れは,チップとカッタボディを組み合わせたときに,ある範囲で変化することによる影響が大きいです.
しかしながら,理論式を作ることはできなくとも,面粗さの大小との関係性が深い数値を,上記した因子のいくつかを考慮することで作ることができます.
その数値の意味を理解してもらうために,いくつかの例を通して説明します.
まず,フライスカッタでの加工によって,加工面が生成される仕組みを説明します.
フライスカッタでは複数の刃先によって,工作物が加工され,そのときに残ったさらい刃による加工痕が加工面として残ります.
単純化したモデルとしては,各切れ刃のさらい刃を一刃送り量ずつずらして並べ,そのさらい刃稜線の最下点を繋ぐものが考えられます.
以降は,このモデルを使って説明を行います.

まず,さらい刃長さ,一刃あたり送り量,刃数の関係性について説明します.
一刃あたり送り量と刃数から一回転送り量が計算できます.
この一回転送り量とさらい刃長さの関係性は,面粗さに大きく影響を及ぼします.
この理由は,最も突出したさらい刃一枚が加工面を仕上げる場合と,複数のさらい刃によって加工面が仕上げられる場合があるためです.
単純には,この2条件がわかれるのは,
最も突出したさらい刃一枚が加工面を仕上げる場合:一回転送り量 <= さらい刃長さ
複数のさらい刃によって加工面が仕上げられる場合:一回転送り量 > さらい刃長さ
という関係性による部分が大きいです.
つまり,一枚の刃しか加工面の生成に影響しないのなら,振れが大きくても,加工面の面粗さは良好になることもあるということです.
従来の振れの評価方法は,これを表現することができません.
その最たるものが,ワイパー刃と呼ばれるものです.
ワイパー刃は,「長いさらい刃を持ち,通常のチップよりも軸方向に突出されることにより,ワイパー刃のみで加工面を仕上げさせ,面粗さを改善する」という作用を持ちます.
そのため,もしワイパー刃を取り付けた状態で,振れを測定した場合,その値は非常に大きくなります.
次に,複数のさらい刃によって加工面が仕上げられる場合を考えます.
まず,8枚刃のフライスカッタを考えます.
一回転送り量は2mm/rev,さらい刃長さは1mmとします.
このとき,以下の2条件の軸方向振れを仮定します.
条件A:1番と2番の刃先が10um突出し,残りはすべて0um.
条件B:1番と5番の刃先が10um突出し,残りはすべて0um.
この場合,どちらの条件のほうが面粗さが良くなるか,ということを考えます.
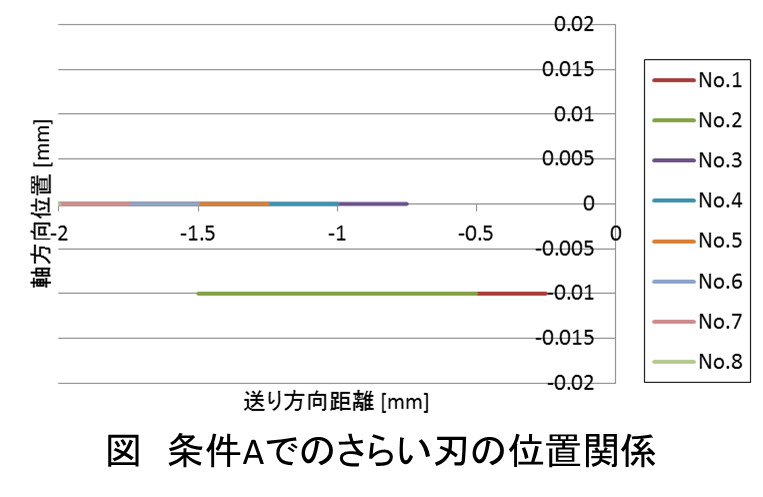
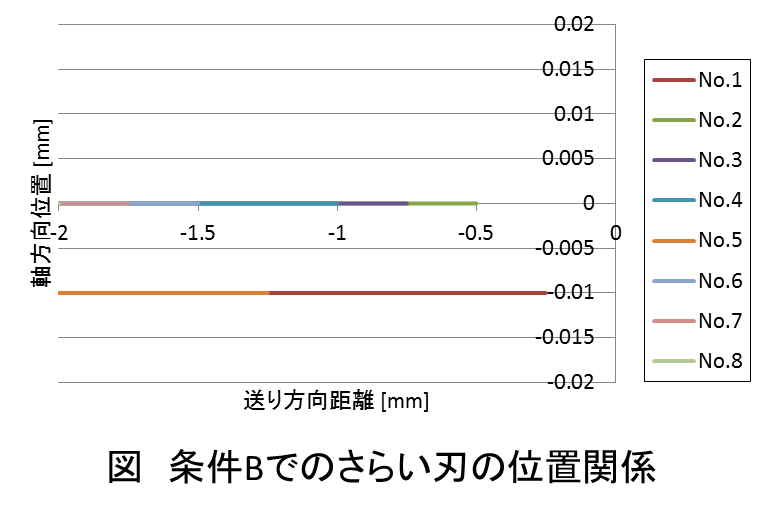
さらい刃長さは1mmしかないので,条件Aでは,1番と2番だけでは,加工面を生成しきることができず,7番と8番の刃先による面が残るため,10umの凹凸が加工面に残ります.
その反面,条件Bでは,1番と5番による,さらい刃の加工面がつながることで,加工面上に凹凸が残りません.
つまり,振れが面粗さに与える影響を考える場合,各切れ刃での振れとさらい刃長さを考慮する必要があります.
こういった影響も,従来の振れの評価方法では表現できていません.
そこで,面粗さへの影響をより表現可能な振れの指標に必要な数値を考えます.
これには,振れ,さらい刃長さ,一刃あたり送り量,刃数を使います.
これらの数値は,市販されているツールプリセッタで測定可能であるため,選定しました.
正確には,さらい刃形状とフェイスアングルも必要ですが,測定が難しく,計算に取り込むのも難しいので除外しました.
振れ,さらい刃長さ,一刃あたり送り量,刃数を使って,上述した各刃の重なりを考慮したうえで,そこから最大値と最小値の差を計算したものを実用軸方向刃振れとしています.
本指標は,数式で単純に表すことが難しく,場合分けが多いので,実用軸方向刃振れとしてアプリで計算できるようにしています.
隣接刃振れのくだりで,切削面積の計算を行いましたが,実際には,軸方向の刃振れの考慮は複雑になります.
そこで,実用軸方向刃振れと同様に,振れ,さらい刃長さ,一刃あたり送り量,刃数を考慮して,切削面積の変化を計算しています.
これも,複雑な場合分けを使って数値を求めているので,計算式として表記できません.